Understanding LEV Inspection South Wales: A Comprehensive Guide
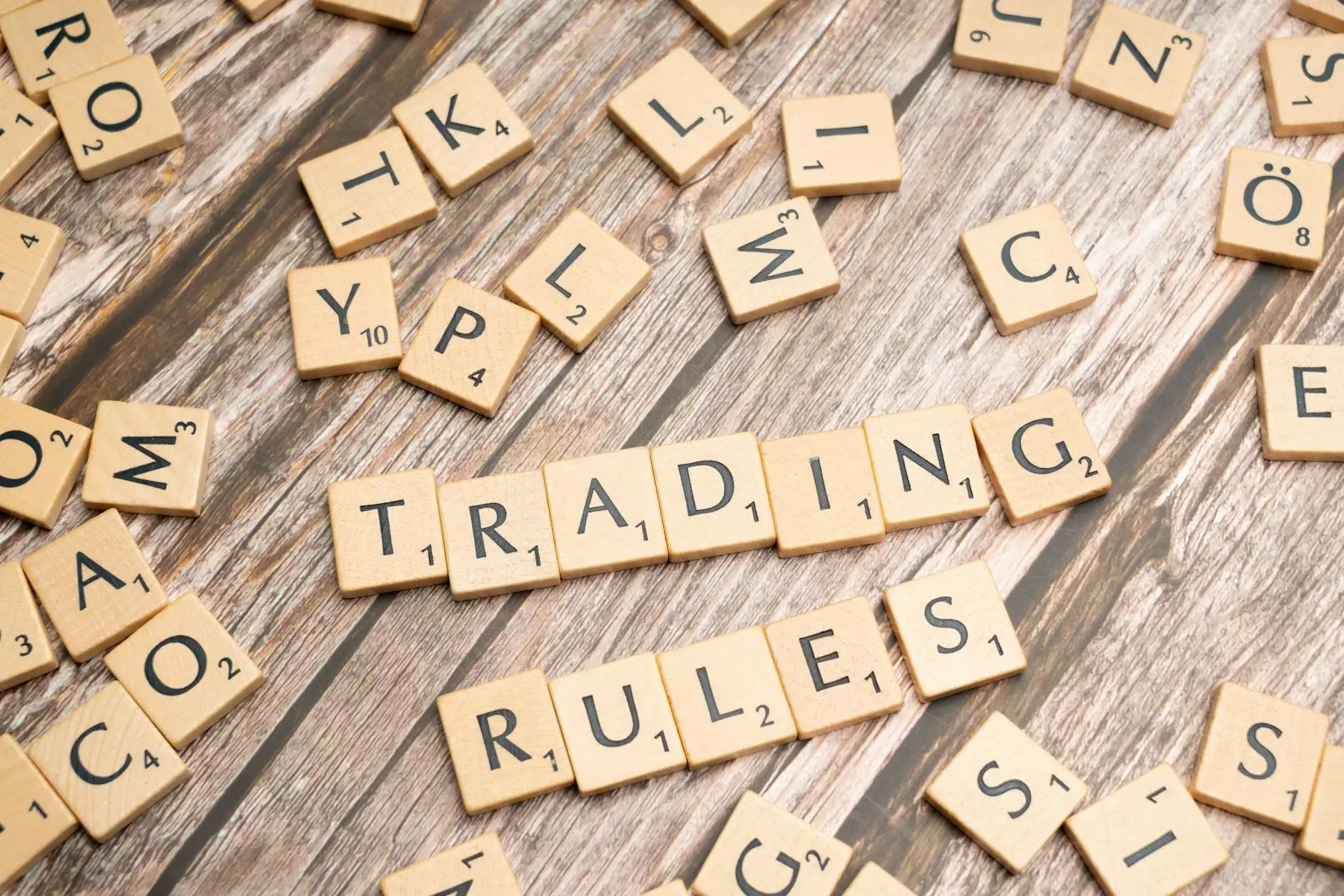
In today's business landscape, compliance with safety regulations is not just a legal obligation; it is vital for the health of your employees and the sustainability of your operations. One area that requires a keen focus is Local Exhaust Ventilation (LEV) systems. In South Wales, conducting thorough LEV inspections is an essential component of maintaining a safe working environment. This article delves deep into the necessity of LEV inspections, the regulations governing them, and the benefits they provide for businesses in the region.
The Importance of LEV Systems
LEV systems are crucial in industries where processes generate airborne pollutants, including:
- Woodworking
- Metal fabrication
- Chemical manufacturing
- Food production
These systems work by capturing harmful substances at their source, thereby preventing them from contaminating the workplace. An effective LEV system can significantly reduce the risk of respiratory diseases and other health issues associated with poor air quality.
Legal Requirements for LEV Inspection in South Wales
Under UK law, employers have a duty to ensure that their workplace is safe and healthy. This includes ensuring that all LEV systems are functioning correctly. The Health and Safety Executive (HSE) outlines specific guidelines for businesses:
- LEV systems must be regularly maintained and inspected at least once every 14 months.
- It is crucial to keep accurate records of inspections and maintenance activities.
- Employers must ensure that employees understand the importance of LEV systems and how to use them effectively.
Failure to comply with these regulations can result in serious legal consequences and increased risks to employee health.
Benefits of Regular LEV Inspections
Consistent LEV inspections yield numerous benefits for South Wales businesses, including:
- Enhanced Worker Safety: Regular inspections help identify and mitigate risks associated with harmful substances.
- Improved Compliance: Staying on top of inspections ensures that your business meets regulatory requirements, avoiding potential fines.
- Increased Efficiency: Well-maintained systems operate more effectively, leading to lower energy costs and improved productivity.
- Boosted Employee Morale: A safe working environment contributes to higher job satisfaction and lower turnover rates.
How to Choose an LEV Inspection Service in South Wales
Selecting the right LEV inspection service is critical for ensuring that your systems are properly evaluated. Here are some key factors to consider:
- Expertise and Certification: Ensure the company has qualified technicians with experience in LEV systems. Look for certifications from recognized industry bodies.
- Comprehensive Services: Choose a service provider that offers a full range of inspections, from assessments to performance testing and maintenance recommendations.
- Reputation: Research the company’s track record and customer reviews to gauge their reliability and responsiveness.
- Cost Transparency: Select a provider that offers clear pricing with no hidden fees, ensuring you understand the costs involved upfront.
The LEV Inspection Process
Understanding the LEV inspection process can help you appreciate the thoroughness required to maintain safety. The process typically involves the following steps:
- Initial Assessment: Technicians evaluate the overall condition of your LEV system, looking for signs of wear, damage, or inconsistency in performance.
- Performance Testing: Each component of the LEV system, including capture rates and airflow measurements, is tested to ensure optimal function.
- Documentation: Comprehensive reports are produced, detailing the findings, compliance status, and recommendations for improvements.
- Follow-Up: Based on findings, the inspection service may provide follow-up assistance to address any identified issues.
Common Challenges in LEV Systems
Many businesses face common challenges regarding LEV systems. Addressing these challenges head-on can lead to better compliance and safety outcomes:
- Inadequate Training: Employees must be trained to use LEV systems properly. Inadequate knowledge can lead to improper use and inefficiency.
- Wear and Tear: Over time, LEV systems can deteriorate. Routine inspections help identify issues before they escalate.
- Neglecting Maintenance: Failing to perform regular maintenance can lead to decreased system performance, necessitating costly repairs or replacements.
Tips to Improve Your LEV System
Beyond inspections, enhancing your LEV system can further ensure safety and compliance. Consider the following tips:
- Regular Training: Conduct regular training sessions for employees to ensure they understand how to use and maintain LEV systems properly.
- Invest in Quality Equipment: Choosing quality systems over the cheapest options can save money in the long run through decreased maintenance and energy costs.
- Conduct Risk Assessments: Regular risk assessments can help identify potential hazards and ensure your LEV systems effectively mitigate them.
The Future of LEV Inspections in South Wales
As industries evolve, so do the requirements surrounding safety and air quality management. The future for LEV inspection in South Wales looks promising, with technological advancements playing a central role. Innovations like smart sensors and automated monitoring systems are emerging, providing real-time data that can enhance compliance and efficiency.
Moving forward, businesses must stay updated with these advancements and adapt their strategies accordingly to maintain the highest safety standards.
Conclusion
Prioritizing LEV inspection South Wales is not just about meeting legal obligations; it signifies a commitment to employee safety and operational excellence. By investing in regular inspections, choosing reputable service providers, and continuously improving your systems, you can create a safer work environment and enhance your business’s reputation. At Safe Plant UK, we specialize in comprehensive LEV inspections and are dedicated to helping you maintain compliance and safety in your operations.