Understanding Plastic Injection Molding Products
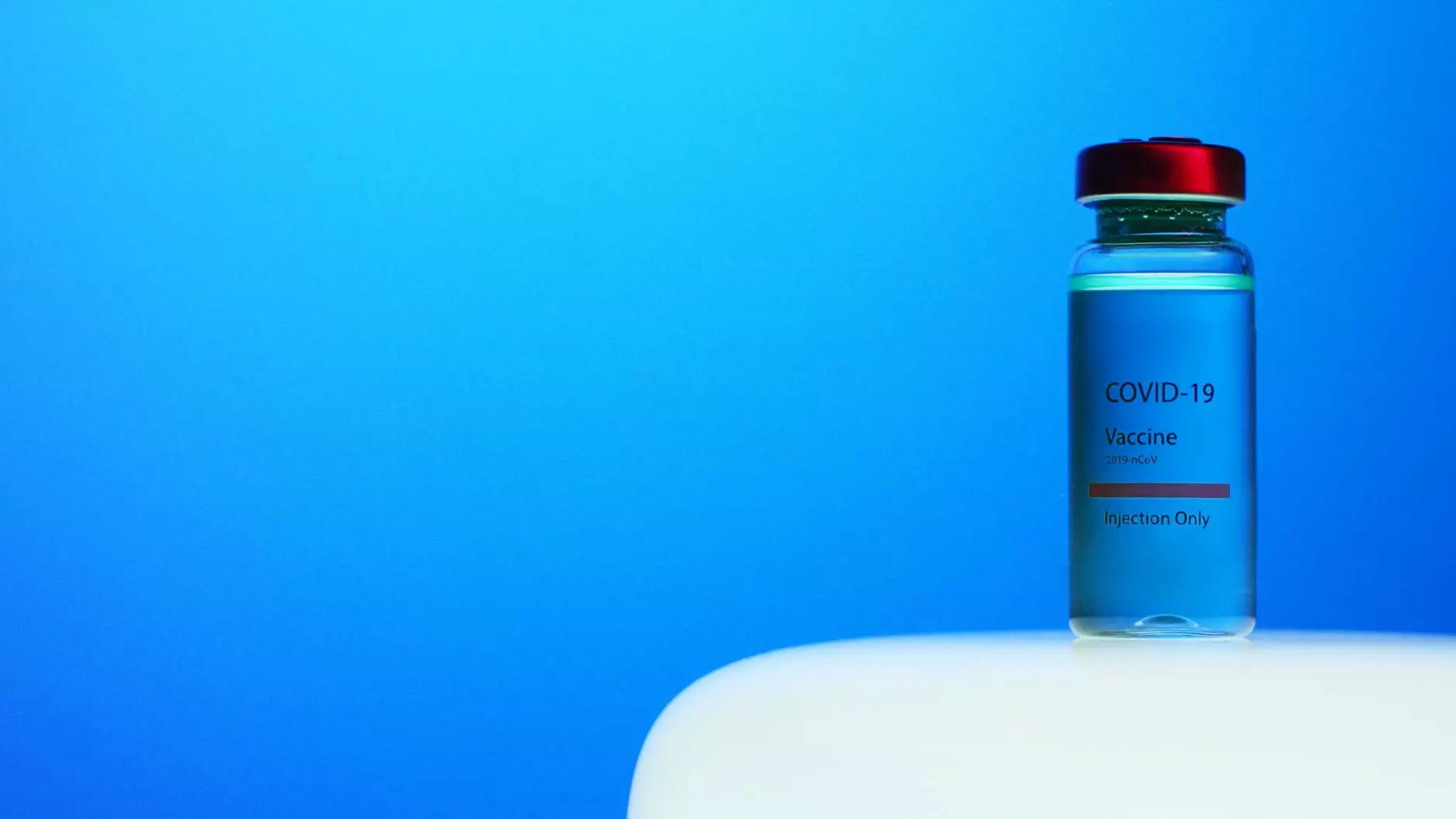
In today's competitive manufacturing landscape, plastic injection molding products play a significant role in production efficiency and product quality. This manufacturing process involves injecting molten plastic into molds to create a variety of shapes and sizes. Given its versatility and efficiency, it has become one of the most popular manufacturing techniques in modern industry.
The Basics of Plastic Injection Molding
Plastic injection molding is a complex process that requires precision, knowledge, and advanced technology. Understanding the fundamentals of this technique is essential for any manufacturer or business that relies on high-quality plastic components.
What is Plastic Injection Molding?
At its core, plastic injection molding is the process of creating parts by injecting molten material into a mold. The basic steps involved include:
- Material Selection: Choosing the right type of plastic resin based on the desired properties.
- Heating and Injection: The plastic is heated until molten and then injected into a mold under high pressure.
- Cooling: The injected plastic cools and solidifies within the mold.
- Ejection: The finished product is ejected from the mold for further processing or assembly.
Materials Used in Plastic Injection Molding
Several types of materials can be used in the plastic injection molding process. Some common materials include:
- Polyethylene (PE): Known for its flexibility and chemical resistance.
- Polypropylene (PP): Valued for its strength and durability.
- Polystyrene (PS): Often used in consumer products due to its affordability.
- Polyvinyl Chloride (PVC): Popular for its versatility and weather resistance.
- Thermoplastic Elastomers (TPE): Combining the characteristics of rubber and plastic.
Advantages of Plastic Injection Molding Products
The benefits of using plastic injection molding products are numerous, making it a preferred choice for many industries. Here are some key advantages:
High Efficiency and Production Rates
Once the initial setup is completed, plastic injection molding processes can produce thousands of identical parts quickly and efficiently. This high production rate makes it an ideal solution for large-scale manufacturing.
Cost-Effectiveness
While the initial costs of designing molds can be high, the overall cost per part declines significantly with higher production volumes. This makes plastic injection molding a cost-effective solution for manufacturers looking to scale operations.
Design Flexibility
Plastic injection molding allows for a high degree of design flexibility. Manufacturers can produce complex shapes and structures that may be impossible with other manufacturing methods. This capability enables businesses to innovate and create unique products tailored to market demands.
Minimal Waste Generation
Another standout feature of this process is the reduced material waste. The injection molding process is highly efficient, with excess material often being recycled. This attribute not only supports sustainability initiatives but also contributes to lower production costs.
Applications of Plastic Injection Molding Products
Plastic injection molding products find use in a wide array of industries. Below are some prominent applications:
Automotive Industry
In the automotive sector, plastic injection molding is widely employed for producing various components such as:
- Dashboard components
- Interior panels
- Exterior trims
- Lightweight structural parts
Consumer Goods
The manufacturing of everyday consumer items heavily relies on plastic injection molding. Common products include:
- Toys and sporting goods
- Kitchenware and appliance housings
- Personal care products
Medical Devices
With stringent standards and regulations, the medical field benefits greatly from precise plastic injection molding. It is used to make:
- Medical instruments
- Device housings and components
- Single-use products such as syringes
Packaging Solutions
Plastic injection molding contributes significantly to the packaging industry with products such as:
- Containers and bottles
- Caps and closures
- Custom packaging solutions
The Future of Plastic Injection Molding Products
As industries evolve, so do the techniques used in creating plastic injection molding products. The future of this manufacturing method is promising, driven by innovation and technology.
Advancements in Materials
New materials, including bio-resins and advanced composites, are being developed to meet the growing demand for sustainable and high-performance products. The integration of these materials into plastic injection molding processes will lead to even more efficient and environmentally friendly production methods.
Automation and Robotics
Automation is transforming manufacturing processes, including plastic injection molding. Incorporating robotics into production lines increases efficiency, reduces human error, and lowers labor costs. As automation continues to advance, companies that produce plastic injection molded products will benefit from increased precision and higher output rates.
Choosing the Right Manufacturer for Plastic Injection Molding Products
When selecting a manufacturer for plastic injection molding products, several factors should be considered:
Experience and Expertise
Choose a company experienced in the industry and knowledgeable about the latest manufacturing techniques. This expertise ensures high-quality outputs and innovative solutions for complex design challenges.
Quality Assurance Processes
A reliable manufacturer implements strict quality control measures. Inquire about their testing methods to ensure that every product meets intended specifications and regulatory standards.
Customer Support and Communication
Effective communication and strong customer support from a manufacturer can make a significant difference in project implementation. Look for companies that are responsive and willing to collaborate closely throughout the process.
Conclusion
In conclusion, plastic injection molding products are indispensable in today's manufacturing sector, offering numerous benefits that include efficiency, cost-effectiveness, and versatility. As industries continue to progress, the potential of plastic injection molding will expand, driven by innovation and advancements in technology. For businesses looking to leverage plastic injection molding, partnering with expert manufacturers such as those found at deepmould.net can lead to successful and sustainable production outcomes.