Understanding the Role of a Hydraulic Tube Fittings Manufacturer
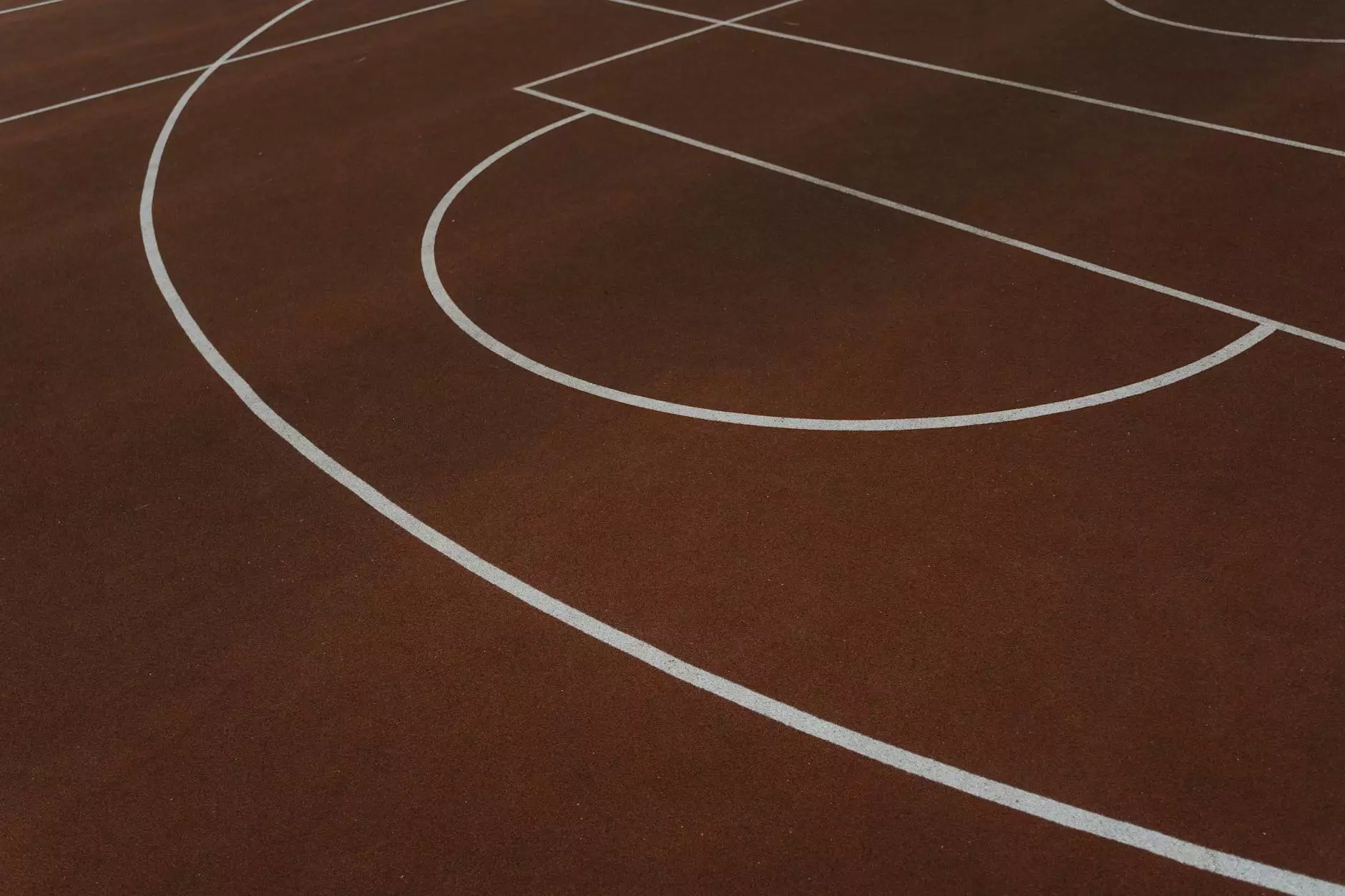
Hydraulic tube fittings play a crucial role in various industries, including construction, automotive, aerospace, and manufacturing. As a Hydraulic Tube Fittings Manufacturer, providing quality fittings is essential to ensure the efficiency and safety of hydraulic systems. In this comprehensive guide, we will delve into the significance of hydraulic tube fittings, their types, applications, and the importance of choosing the right manufacturer.
What are Hydraulic Tube Fittings?
Hydraulic tube fittings are essential components that form a connection between tubes and hydraulic systems. They are designed to maintain pressure and ensure the flow of fluids within hydraulic lines. The reliability of these fittings is pivotal in ensuring a leak-proof operation, which is why the selection of a reputable hydraulic tube fittings manufacturer is of utmost importance.
Types of Hydraulic Tube Fittings
There are various types of hydraulic tube fittings, each serving a specific function and application. Understanding these different types can aid in selecting the right fittings for your hydraulic systems:
- Compression Fittings: Used to secure tubing by compressing it against the fitting. Ideal for high-pressure systems.
- Bolt and Nut Fittings: Provide a strong connection, commonly used in high-pressure applications.
- Flare Fittings: Feature a conical shape that creates a tight seal when connected. Suitable for a variety of applications.
- Barbed Fittings: Excellent for low-pressure applications and flexible tubing.
- Quick Connect Fittings: Allow for easy and fast connection/disconnection of hydraulic lines without tools.
The Importance of Quality in Hydraulic Fittings
The quality of hydraulic tube fittings directly impacts the performance and longevity of hydraulic systems. Here are some reasons why quality is paramount:
- Leak Prevention: High-quality fittings are designed to create secure seals that prevent leaks, vastly reducing the risk of fluid loss and potential hazards.
- Pressure Resistance: Quality fittings can withstand high pressure without failure, ensuring the integrity of the hydraulic system.
- Durability: Robust materials and precise manufacturing processes contribute to the longevity of the fittings.
- Safety: Reliable hydraulic systems minimize risks to personnel and equipment, promoting a safer work environment.
Choosing the Right Hydraulic Tube Fittings Manufacturer
Selecting the right manufacturer is critical to obtaining quality hydraulic tube fittings. Here are some factors to consider:
- Experience and Reputation: Opt for manufacturers with a proven track record in the industry. Research customer testimonials and case studies.
- Material Quality: Inquire about the materials used in their fittings. High-grade materials ensure better performance and safety.
- Certifications: Look for manufacturers that adhere to industry standards and have the necessary certifications (e.g., ISO, SAE).
- Variety of Products: A reputable manufacturer should offer a wide range of fittings to meet diverse application needs.
- Customer Service: Exceptional customer support is essential for addressing technical queries and ensuring customer satisfaction.
Innovations in Hydraulic Tube Fittings
As technology advances, the hydraulic tube fittings industry continues to evolve. Innovations are making hydraulic systems more efficient and user-friendly. Some notable trends include:
- Smart Fittings: Integrated sensors in fittings provide real-time data on pressure and flow, allowing for predictive maintenance.
- Environmentally Friendly Materials: Manufacturers are increasingly using recyclable materials to create sustainable hydraulic fittings.
- 3D Printing: This technology is enabling the rapid prototyping of custom fittings, catering to specific client needs.
Applications of Hydraulic Tube Fittings
Hydraulic tube fittings find applications across various sectors. Here are some of the most prominent areas:
- Automotive: Used in braking systems, power steering, and hydraulic lifts.
- Construction: Essential for heavy machinery, excavators, and cranes that rely on hydraulic power.
- Aerospace: Found in aircraft systems to manage hydraulic fluids and ensure operational safety.
- Manufacturing: Used in automated systems and machinery for efficient production processes.
How to Maintain Hydraulic Tube Fittings
Proper maintenance ensures the longevity and effectiveness of hydraulic tube fittings. Here are some tips for upkeep:
- Regular Inspections: Conduct frequent checks for signs of wear, leaks, or corrosion.
- Cleanliness: Maintain a clean work environment to prevent contaminants from entering the hydraulic system.
- Proper Torque Settings: Ensure fittings are tightened to the recommended torque specifications to prevent loosening over time.
- Fluid Quality: Use high-quality hydraulic fluids and replace them as required to minimize wear.
Conclusion
In conclusion, the role of a Hydraulic Tube Fittings Manufacturer is indispensable in ensuring the safety and efficiency of hydraulic systems across various industries. Selecting high-quality fittings from a reputable manufacturer is crucial for operational success. As technology continues to evolve, staying updated on the latest innovations and maintenance practices will further enhance the longevity and performance of hydraulic systems. Remember, when choosing hydraulic tube fittings, quality should always be a priority.
Hydraulic Tube Fittings Manufacturer