Precision Molds: The Cornerstone of Quality Metal Fabrication
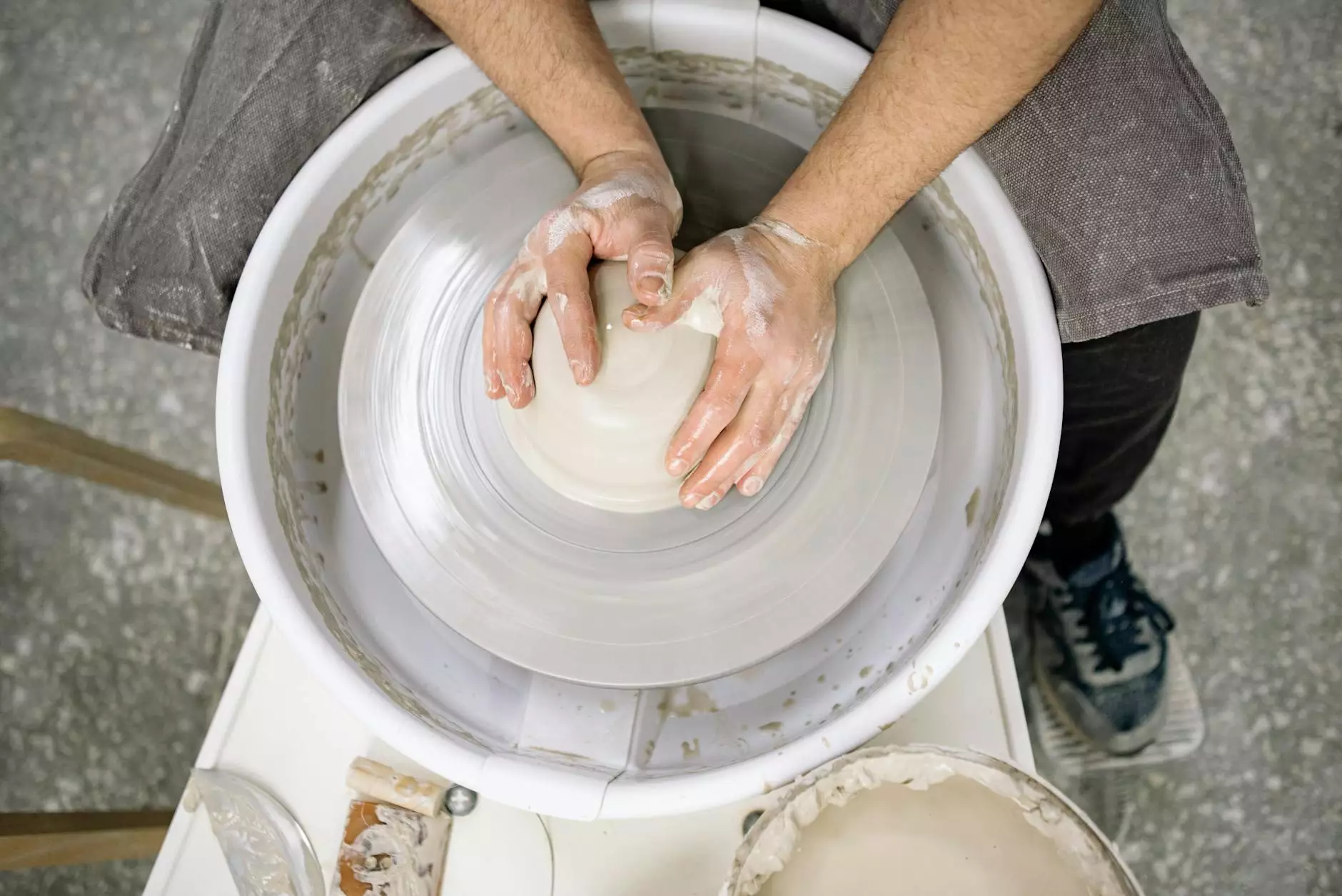
In today's competitive manufacturing landscape, precision molds play a vital role in ensuring superior product quality and operational efficiency. As industries evolve and demand for complex shapes and intricate designs increases, the significance of high-quality molds cannot be overstated. This article explores precision molds, their importance in the metal fabrication sector, and how companies like DeepMould.net are revolutionizing the way we think about mold-making.
Understanding Precision Molds
Precision molds are specialized tools used for shaping materials into specific forms. They are essential in a variety of manufacturing processes, particularly in metal fabrication. These molds ensure that products are manufactured with high precision, resulting in reduced waste and improved efficiency. The following are key characteristics of precision molds:
- High Accuracy: They are designed to produce parts that meet exact specifications.
- Durability: Made from robust materials, precision molds withstand repeated use without degrading.
- Complexity: Capable of creating intricate designs that would otherwise be difficult to achieve.
- Cost-Effectiveness: High-quality molds reduce the need for rework and scrap materials, saving money in the long run.
The Manufacturing Process of Precision Molds
Creating precision molds is a meticulous process that combines advanced technology with skilled craftsmanship. The manufacturing process generally includes the following stages:
1. Design Phase
Every successful mold starts with a comprehensive design. Engineers use computer-aided design (CAD) software to create a digital prototype. This stage is crucial, as it allows for modifications before physical production begins. Designers focus on ensuring that all specifications for the final product are met.
2. Material Selection
Choosing the right materials is critical for the longevity and performance of molds. Common materials used include:
- Steel: Often used for its strength and durability.
- Aluminum: Preferred for lightweight applications and faster production times.
- Thermoplastics: Used for shorter production runs due to their lower cost.
3. Machining and Fabrication
Once the design is finalized and materials selected, the machining process begins. This might involve:
- CNC Machining: This automated process ensures high accuracy and repeatability.
- EDM (Electrical Discharge Machining): Useful for creating complex shapes that are hard to machine with traditional techniques.
- Grinding: Adding the final touches to ensure smooth surfaces and tight tolerances.
4. Assembly and Testing
After machining, the various components are assembled carefully. This stage may also involve testing the molds to ensure they perform as expected and meet quality standards. Adjustments are made as necessary, which is critical to minimize defects in the final products.
Applications of Precision Molds in Metal Fabrication
Precision molds find applications in various sectors, making them indispensable in metal fabrication:
Aerospace Industry
In aerospace manufacturing, precision is non-negotiable. Molds used to create components for aircraft must meet stringent safety and performance standards. This requires molds that can produce lightweight yet strong parts with exacting tolerances.
Automotive Sector
The automotive industry relies heavily on precision molds for manufacturing various components, from body panels to intricate engine parts. The move towards electric vehicles, for instance, has led to new designs that require innovative molding solutions.
Consumer Electronics
With the rapid evolution of technology, the demand for precision molds in consumer electronics is ever-growing. Molds are needed for complex interior components in devices such as smartphones and laptops, allowing for sleek and efficient design.
The Impact of Precision Molds on Manufacturing Efficiency
Utilizing precision molds enhances overall manufacturing efficiency in several ways:
- Reduced Waste: By ensuring accurate dimensions from the outset, manufacturers minimize material waste.
- Faster Production Times: High-quality molds often lead to quicker cycles and reduced downtime.
- Improved Product Quality: Consistency in production translates into higher quality products with fewer defects, increasing customer satisfaction.
Choosing the Right Precision Molds Provider
When selecting a provider for precision molds, manufacturers should consider several factors to ensure that they partner with a reliable source:
Experience and Expertise
Look for providers with extensive experience in the field. Companies like DeepMould.net stand out due to their professional approach and deep understanding of the industry’s requirements.
Technology and Innovation
Providers that utilize the latest technology in mold-making are more likely to deliver products that meet modern manufacturing demands. CNC machineries, 3D printing, and advanced simulation software are indicators of a company's commitment to quality.
Customer Support
Strong customer support can make a significant difference in your experience. An ideal provider assists throughout the process, from initial consultation through the delivery of the final product, ensuring that any issues are addressed promptly.
Future Trends in Precision Molds
The field of precision molds is ever-evolving, with new technologies and methodologies on the horizon. Some future trends include:
Increased Use of Automation
Manufacturers are increasingly adopting automation in the mold-making process. Automated systems enhance precision and speed, resulting in reduced labor costs and improved output.
3D Printing for Prototyping
3D printing technology is revolutionizing how prototypes for molds are created. It allows for rapid prototyping, enabling design verification before the actual mold is produced, which can significantly reduce lead times.
Sustainability Initiatives
With the growing emphasis on sustainability, the mold-making industry is exploring ecological materials and low-energy processes. Providers that focus on sustainable practices not only contribute to environmental stewardship but also appeal to an eco-conscious market.
Conclusion
Investing in precision molds is essential for manufacturers who aim to enhance product quality and operational efficiency. As industries continue to evolve, the demand for precision molds will only increase. Companies like DeepMould.net play a critical role in this landscape, offering innovative solutions that cater to diverse manufacturing needs. By choosing the right provider and embracing emerging technologies, businesses can ensure their competitive edge and set the foundation for success in the ever-changing market.