Precision Plastic Injection: A Game Changer in Modern Manufacturing
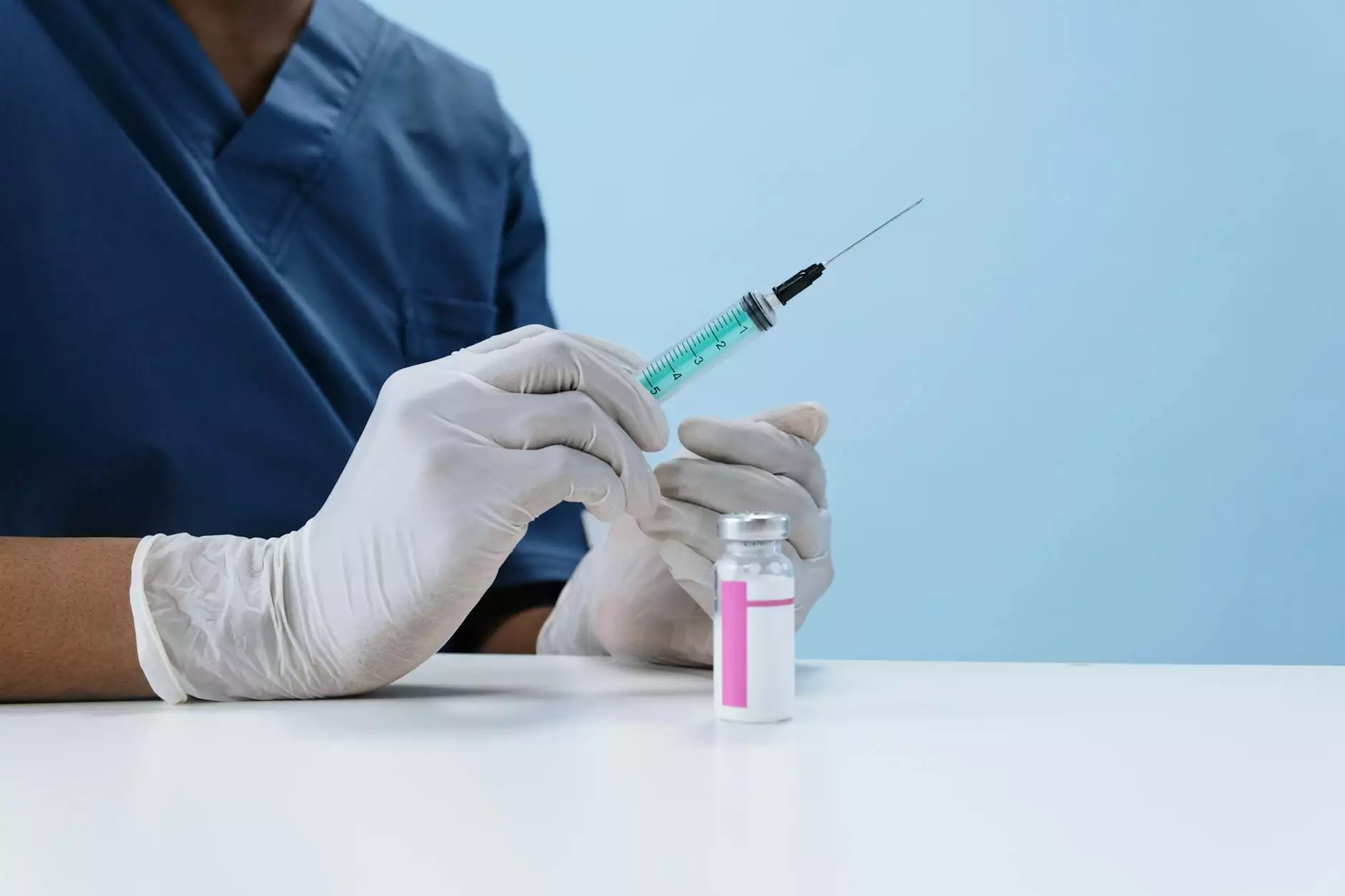
Precision plastic injection is not merely a manufacturing technique; it represents a revolution in the way we conceptualize and produce plastic components. This advanced method allows for the creation of intricate designs and high-volume production with unparalleled efficiency. In this article, we will explore the various facets of precision plastic injection, its applications, and why it stands as a cornerstone of innovation within the metal fabrication sector, particularly as offered by industry leaders such as DeepMould.
Understanding Precision Plastic Injection
At its core, precision plastic injection refers to the process of injecting molten plastic into a mold to produce parts that require high levels of detail and consistency. This method is prized for its ability to create complex geometries that are otherwise challenging to achieve with traditional manufacturing techniques.
How the Process Works
The precision plastic injection process can be broken down into several key stages:
- Material Selection: The process begins with selecting the appropriate thermoplastic material based on the desired properties of the final product.
- Injection Molding: Molten plastic is injected into a pre-designed mold at high pressure, enabling the material to fill all cavities and nuances of the mold.
- Cooling: Upon injection, the plastic cools and solidifies, taking the shape of the mold. This phase is crucial, as it affects the final quality of the part.
- Mold Release: Once sufficiently cooled, the mold opens, and the finished component is ejected. This can happen in a matter of seconds for high-volume production runs.
Benefits of Precision Plastic Injection
The advantages of using precision plastic injection are extensive, making it an increasingly popular choice among manufacturers across various sectors. Here are some of the most significant benefits:
1. High Precision and Accuracy
One of the most celebrated attributes of this manufacturing process is its high precision. The method allows for tolerances as tight as ±0.01mm, ensuring that every part produced meets strict specifications, which is vital in industries such as automotive and aerospace.
2. Cost-Effective Production
Although the initial setup cost for molds can be considerable, precision plastic injection is a cost-effective solution for large production volumes. Once the molds are created, the cost per unit decreases significantly, making it economical for mass manufacturing.
3. Material Versatility
This technique accommodates a wide array of materials, including:
- Polypropylene
- Polyethylene
- Polystyrene
- Thermoplastic elastomers
- Engineering plastics like ABS and nylon
4. Minimal Waste
Compared to traditional machining methods, which can leave behind significant scrap material, precision plastic injection is an efficient process that generates little waste, aligning well with modern sustainability goals.
Applications of Precision Plastic Injection
This method has far-reaching applications across various industries:
Automotive Industry
In the automotive sector, precision plastic injection is used for creating lightweight components that are essential for improving vehicle efficiency. Parts such as dashboards, bumpers, and various interior components are commonly manufactured using this technique.
Medical Devices
The medical industry heavily relies on precision plastic injection to produce components for devices that require stringent quality control and hygiene standards. Items such as surgical instruments, containers for pharmaceuticals, and intricate device housings are often created using this technology.
Consumer Electronics
With the prevalence of technology, consumer electronics have become a significant domain for precision plastic injection. This method is ideal for producing cases, buttons, and other detailed components that require high performance and aesthetic appeal.
The Role of DeepMould in Precision Plastic Injection
DeepMould stands at the forefront of the precision plastic injection landscape. With years of experience in metal fabrication and a keen understanding of how to optimize production, DeepMould offers unique advantages:
Expert Team
The team at DeepMould comprises industry experts who possess extensive knowledge in metal fabrication and precision plastic injection. Their expertise ensures that every project receives the highest level of care and precision.
State-of-the-Art Technology
Using the latest machinery and technology, DeepMould can deliver exceptional results. Their injection molding machines are equipped with advanced controls that allow for fine-tuning of various parameters, ensuring top quality.
Customized Solutions
DeepMould understands that every client has specific needs. They offer tailored solutions to meet unique project requirements, whether for small businesses or large-scale enterprises, ensuring that clients receive products that are perfect fits for their applications.
Challenges and Solutions in Precision Plastic Injection
While precision plastic injection offers numerous benefits, it is not without its challenges. Here, we will discuss common obstacles and how experienced manufacturers like DeepMould can mitigate these issues.
Complexity of Design
As designs become more intricate, the challenges associated with creating molds can increase. However, DeepMould employs advanced CAD/CAM software to simulate and test designs before physical production, reducing the risk of costly errors.
Material Limitations
Not all plastics behave the same under various conditions. DeepMould works with leading suppliers to ensure access to a variety of materials, enabling them to select the best one suited for each application while ensuring compliance with regulatory standards.
Production Speed vs. Quality
Striking a balance between production speed and achieving high-quality outcomes can be challenging. DeepMould utilizes automation technology alongside expert quality control measures to monitor production closely, ensuring that no batch leaves the facility without thorough inspection.
The Future of Precision Plastic Injection
The future appears bright for precision plastic injection. With advancements in technology such as 3D printing and IoT, this method is evolving and integrating more scientific approaches to enhance its efficiency further. Manufacturers like DeepMould are continuously innovating to ensure they remain at the cutting edge of industry practices.
Digital Transformation and Smart Manufacturing
The incorporation of smart technology in manufacturing processes promises greater efficiency and cost savings. Digital twins, AI, and machine learning algorithms are becoming integral in making predictive assessments which help streamline processes and reduce downtime.
Sustainability Initiatives
As the demand for environmentally friendly production methods increases, precision plastic injection is already aligned with these sustainability goals. Continuous improvement in recycling processes and material efficiency will aid in meeting regulatory requirements while also satisfying consumer demands for greener options.
Conclusion
In conclusion, precision plastic injection is a vital process that transforms the way manufacturers produce components across multiple industries. With companies like DeepMould leading the charge in quality and innovation, the potential for growth and advancement in this field remains limitless. As we continue to embrace technology and sustainability, the role of precision plastic injection will only become more significant.