Elevating Manufacturing: The Role of Rapid Injection Molding Prototyping
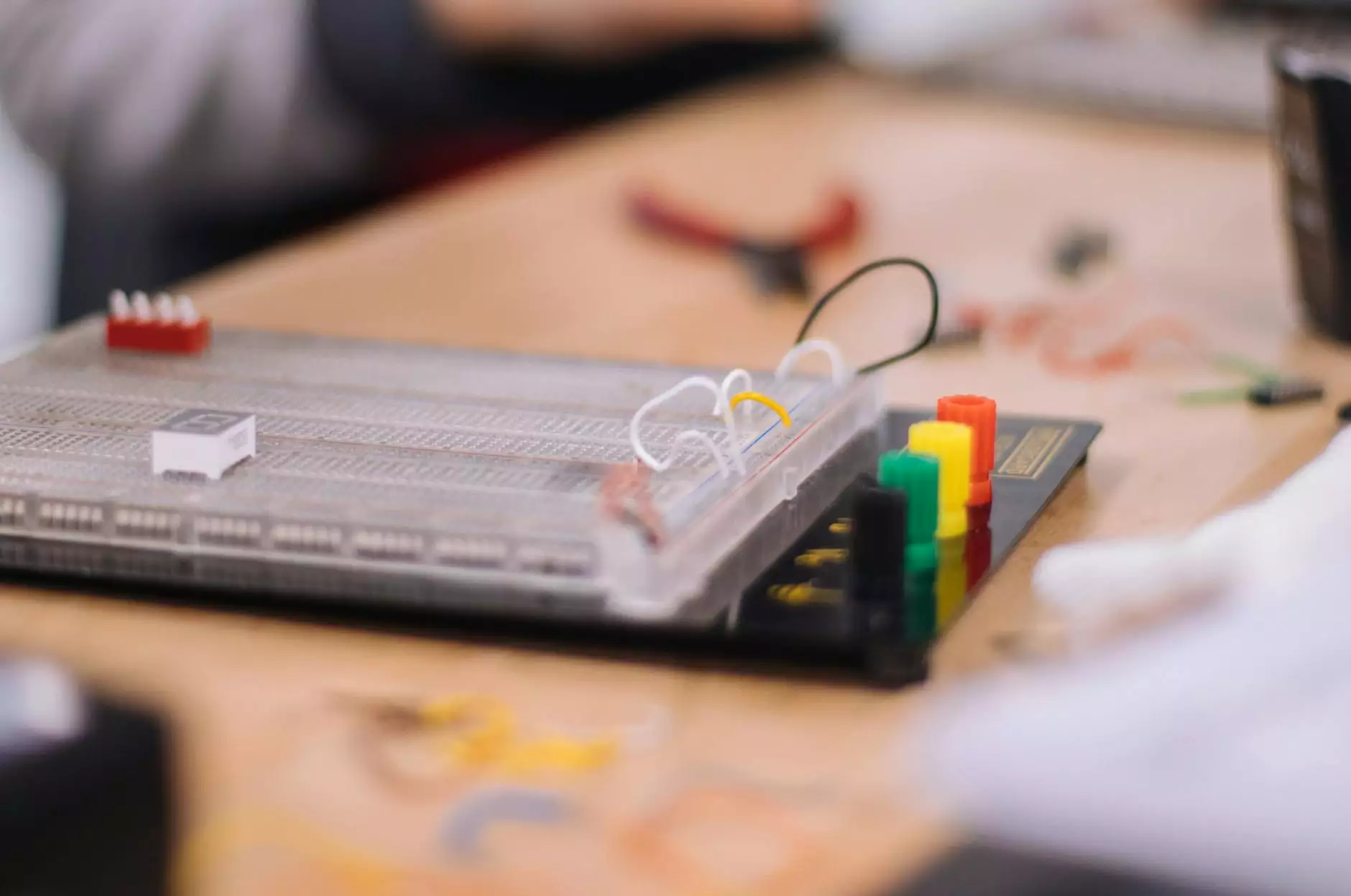
In today's competitive landscape, businesses are vying for an edge in innovation and efficiency. Among the myriad ways to achieve this, one standout method is rapid injection molding prototyping. This advanced manufacturing technique significantly shortens the production cycle, allows for iterative design changes, and ultimately reduces costs associated with traditional prototyping methods. As companies like DeepMould.net lead the charge in metal fabrication, understanding and leveraging the benefits of rapid injection molding becomes paramount.
Understanding Rapid Injection Molding Prototyping
Rapid injection molding prototyping combines the principles of traditional injection molding with accelerated processes to produce prototypes quickly and efficiently. This technique is not merely a faster version of traditional methods; it incorporates unique approaches that optimize both speed and quality in prototyping. The core process involves injecting molten material into a mold to form a specific shape, allowing manufacturers to create accurate representations of their final products.
Key Features of Rapid Injection Molding
- Speed: Reduces lead times significantly, with prototypes available within days rather than weeks.
- Cost-Effectiveness: Lowers manufacturing costs due to reduced material waste and faster production cycles.
- Precision: Ensures high accuracy in the prototype, making it a reliable representation of the final product.
- Flexibility: Allows for easy modifications, enabling designers to iterate without excessive expenses.
The Importance of Prototypes in the Manufacturing Process
Prototyping plays a critical role in the overall manufacturing process. It serves as a preliminary version of a product that can be tested, refined, and modified. By utilizing rapid injection molding prototyping, businesses can:
- Verify design concepts before committing to full-scale production.
- Identify potential issues or areas for improvement early in the development process.
- Reduce time-to-market for new products, providing a competitive advantage.
- Gain valuable feedback from stakeholders, including customers and engineers.
Applications of Rapid Injection Molding Prototyping in Metal Fabrication
The metal fabrication industry thrives on innovation and efficiency, making rapid injection molding prototyping particularly beneficial. This section explores how this technology is being applied across various sectors:
1. Automotive Industry
In the automotive sector, speed and precision are of the essence. Rapid injection molding allows manufacturers to produce high-quality prototypes for components such as dashboards, casings, and trim pieces. By quickly validating designs, companies can adjust aesthetic and functional elements before full production begins, thus ensuring the final product meets safety and regulatory standards.
2. Aerospace Sector
The aerospace industry demands the highest levels of accuracy and performance. Rapid injection molding prototyping enables aerospace engineers to prototype components like brackets and housings effectively. The ability to test parts under real-world conditions helps to ensure safety and compliance with stringent industry regulations, ultimately leading to more reliable aircraft designs.
3. Consumer Electronics
Consumer electronics manufacturers consistently seek to reduce time-to-market. Utilizing rapid injection molding, prototyping for device housings and internal components can be achieved swiftly. The iterative process allows for quick adjustments based on market feedback, ensuring that products are not only functional but also aesthetically pleasing to consumers.
4. Medical Devices
In the medical realm, the stakes are high, and the need for precise, functional prototypes is critical. With rapid injection molding, manufacturers can create prototypes for surgical instruments, enclosures, and other medical devices significantly faster. This agility helps to ensure that new devices are both effective and ready for market approval in record time.
Benefits of Rapid Injection Molding: Why Your Business Should Adapt
As industries evolve, adapting to new technologies is essential. Here are some compelling reasons why businesses should embrace rapid injection molding prototyping:
- Reduced Timeframes: Speed up your design cycle, allowing you to respond to market needs more swiftly.
- Lower Costs: With fewer resources wasted on traditional prototyping methods, save on material and labor costs.
- Iterative Testing: Allow for multiple rounds of testing and feedback, which can refine your product before launch.
- Enhanced Market Understanding: Quick prototypes enable real-world testing, gathering crucial data on usability and design.
Overcoming Challenges in Rapid Injection Molding Prototyping
While the advantages of rapid injection molding prototyping are numerous, businesses may encounter specific challenges. Understanding these challenges can prepare companies to devise effective strategies for overcoming them:
1. Material Limitations
Not all materials are suitable for rapid injection molding. It is essential to choose materials that can withstand the pressures of the injection process while still providing the desired properties in the final product. Collaboration with material suppliers can drastically widen options while meeting necessary specifications.
2. Complex Geometries
While rapid injection molding can accommodate many designs, extremely complex geometries may still pose challenges. Engaging experienced engineers in the design phase can ensure that designs remain practical and manufacturable, reducing the likelihood of complications during production.
3. Tooling Costs
Though rapid injection molding is generally more cost-effective than traditional methods, initial tooling costs can still be significant. Companies can mitigate these costs through effective design techniques and negotiating with suppliers to ensure competitive pricing on tooling production.
The Future of Rapid Injection Molding Prototyping
The landscape of manufacturing is continuously changing, and the future of rapid injection molding prototyping looks promising. Innovations in materials, techniques, and machinery are paving the way for even smarter and more efficient production processes. As industries demand quicker turnarounds and higher quality, businesses that invest in these advanced methods are likely to lead in their respective markets.
Embracing Technological Advancements
Future developments in biocompatible materials and smart manufacturing systems will enable even more unprecedented applications for rapid injection molding. As technology continues to evolve, staying ahead of the curve is essential for any forward-thinking business in the metal fabrication sector.
Sustainability and Environmental Considerations
As sustainability becomes a growing focus across all industries, rapid injection molding presents opportunities for greener production practices. Investments in sustainable materials and energy-efficient processes can help fabrication businesses to position themselves as environmentally responsible leaders.
Conclusion: The Path Forward with Rapid Injection Molding Prototyping
In an era marked by innovation, foresight, and a relentless pursuit of efficiency, rapid injection molding prototyping has emerged as a game-changing process in the realm of manufacturing. Companies like DeepMould.net are at the forefront of this revolution, redefining what's possible in metal fabrication. By harnessing the advantages of this powerful prototyping method, businesses can not only enhance their operational efficiency but also improve product quality, accelerate their market readiness, and ultimately, secure a substantial competitive advantage. Now is the time to explore this innovative approach—to thrive in a fast-paced world where adaptability and speed are paramount.