The Ultimate Guide to Disposable Mask Making Machines
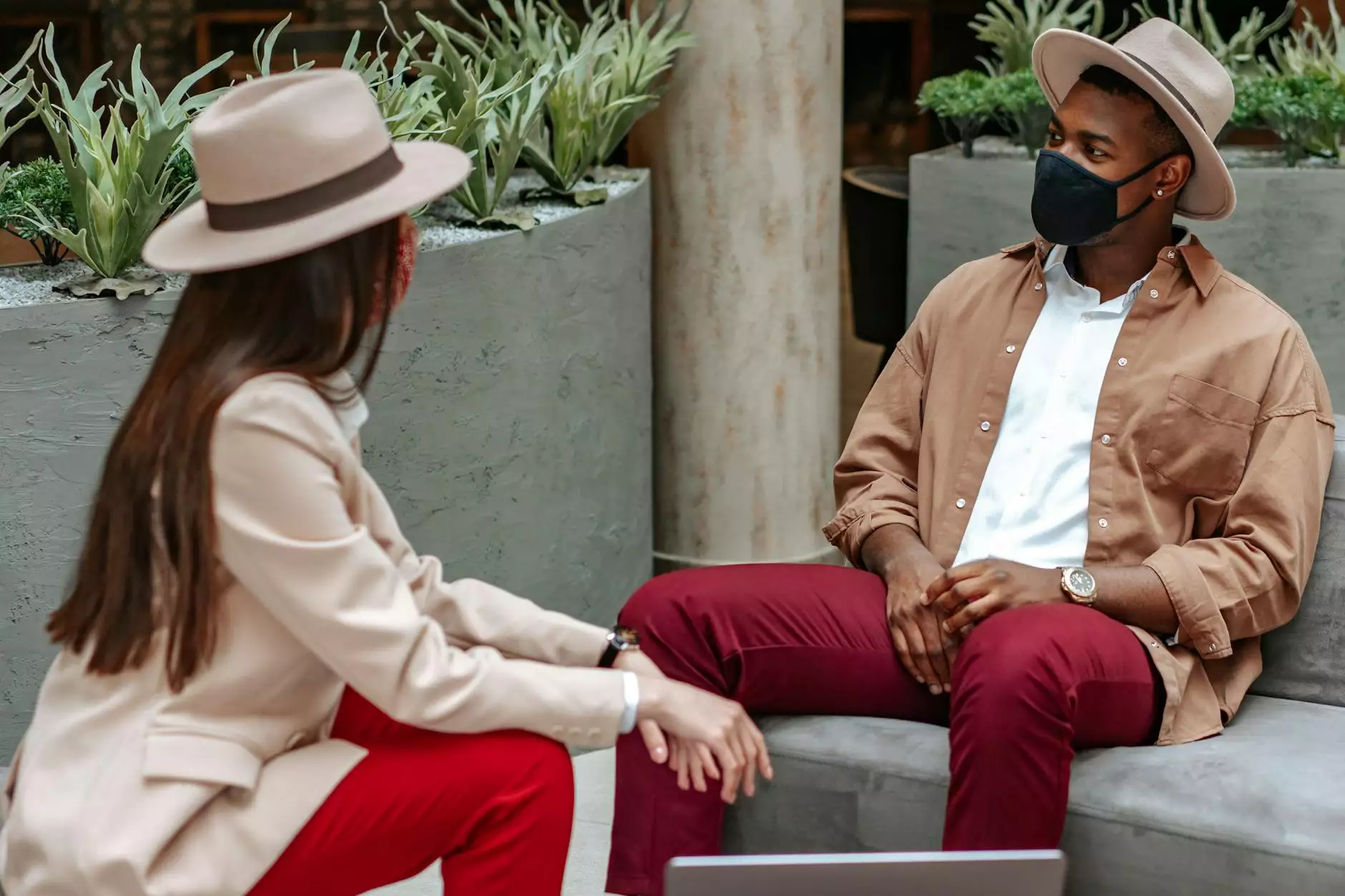
In today’s world, the importance of personal protective equipment (PPE) has skyrocketed, with the disposable mask making machine becoming an essential tool for manufacturers and businesses. Understanding this machinery is crucial for anyone looking to enter the PPE market. This comprehensive guide will explore the features, benefits, and various aspects of disposable mask making machines, providing you with all the information you need to make an informed decision for your business.
What is a Disposable Mask Making Machine?
A disposable mask making machine is a specialized piece of equipment designed to produce face masks that can be easily discarded after use. These machines automate the entire mask production process, ensuring high output and maintaining quality standards. With the rise in demand for masks, these machines are proving to be a lucrative investment for businesses worldwide.
Types of Disposable Mask Making Machines
When it comes to disposable mask making machines, various types are available, each suited for different production needs. Here are some common types:
- Fully Automatic Disposable Mask Making Machine: This machine can perform all functions from feeding materials to packaging automatically, ideal for large-scale production.
- Semi-Automatic Mask Making Machine: While it requires some manual input, this type is still efficient for smaller operations or businesses just starting.
- Mask Inner Earloop Welding Machine: Designed specifically for welding the earloops onto masks, this machine ensures durability and comfort for the user.
- Mask Folding Machine: This focuses on creating three-dimensional masks, providing better fit and comfort for the wearer.
How Does a Disposable Mask Making Machine Work?
The operation of a disposable mask making machine involves several key steps:
- Material Feeding: The process begins with the automatic feeding of non-woven fabric rolls into the machine.
- Cutting: The fabric is then cut into the required mask shape and size.
- Ultrasonic Welding: Next, ultrasonic waves are used to bond the layers of the mask together, ensuring that the masks are secure and durable.
- Ear Loop Attachment: After the mask body is formed, ear loops are attached using precision welding.
- Folding: The masks might be folded to facilitate easier packaging and distribution.
- Packaging: Finally, finished masks are automatically packaged for shipment.
Benefits of Investing in Disposable Mask Making Machines
Investing in a disposable mask making machine comes with several advantages that can significantly benefit your business, such as:
- High Production Capacity: These machines can produce thousands of masks per hour, meeting high demand efficiently.
- Cost-Effective: Automating the manufacturing process reduces labor costs and minimizes material waste, leading to higher profit margins.
- Quality Assurance: With advanced technology, these machines maintain consistent quality and meet health standards.
- Versatility: Many machines can produce different kinds of masks, including surgical masks and general-use masks.
- Market Demand: With ongoing global health concerns, the market for disposable masks remains robust, providing a stable revenue source.
Choosing the Right Disposable Mask Making Machine
When selecting a disposable mask making machine, consider the following:
- Production Volume: Assess how many masks you plan to produce daily and choose a machine that meets your capacity needs.
- Machine Specifications: Look at the specific functionalities such as speed, size, and usability of the machine.
- Supplier Reputation: Research the manufacturer, like ShineBenMach, to ensure they have a good track record and provide reliable support.
- After-Sales Support: Check if the supplier offers maintenance services and readily available spare parts.
- Cost-Effectiveness: Balance cost with features; sometimes a cheaper machine might not provide the best long-term value.
Implementing and Operating Your Disposable Mask Making Machine
Once you've acquired your disposable mask making machine, you need to consider its implementation and operation thoroughly. Here are some essential steps:
Training Your Staff
Proper training for your staff is vital to operate the machinery efficiently. Investing time in training ensures:
- Staff can troubleshoot minor issues.
- Maximal output is achieved from the machine.
- Quality standards are maintained throughout the production process.
Regular Maintenance
To ensure longevity and performance, regular maintenance of your machine is crucial. Key maintenance practices include:
- Cleaning and lubricating moving parts.
- Regularly checking and replacing worn parts.
- Conducting performance audits to ensure optimal operation.
Market Trends and Future Opportunities
The demand for masks is expected to continue evolving. Understanding market trends will help you navigate this dynamic landscape. Some emerging trends include:
- Increased Demand for Fashion Masks: Customization and aesthetics in masks are gaining popularity.
- Integration with Technology: Products like masks with sensors for health monitoring are being developed.
- Sustainable Materials: There is a shift towards eco-friendly materials in mask production.
Conclusion
In conclusion, investing in a disposable mask making machine represents a fantastic opportunity in today’s PPE market. By understanding the operation, benefits, types, and implementation of these machines, businesses can position themselves strategically. As health consciousness continues to shape consumer behavior, those equipped with the right technology will undoubtedly thrive. For more information and a closer look at high-quality mask making machinery, consider reaching out to ShineBenMach for expert guidance and superior products.